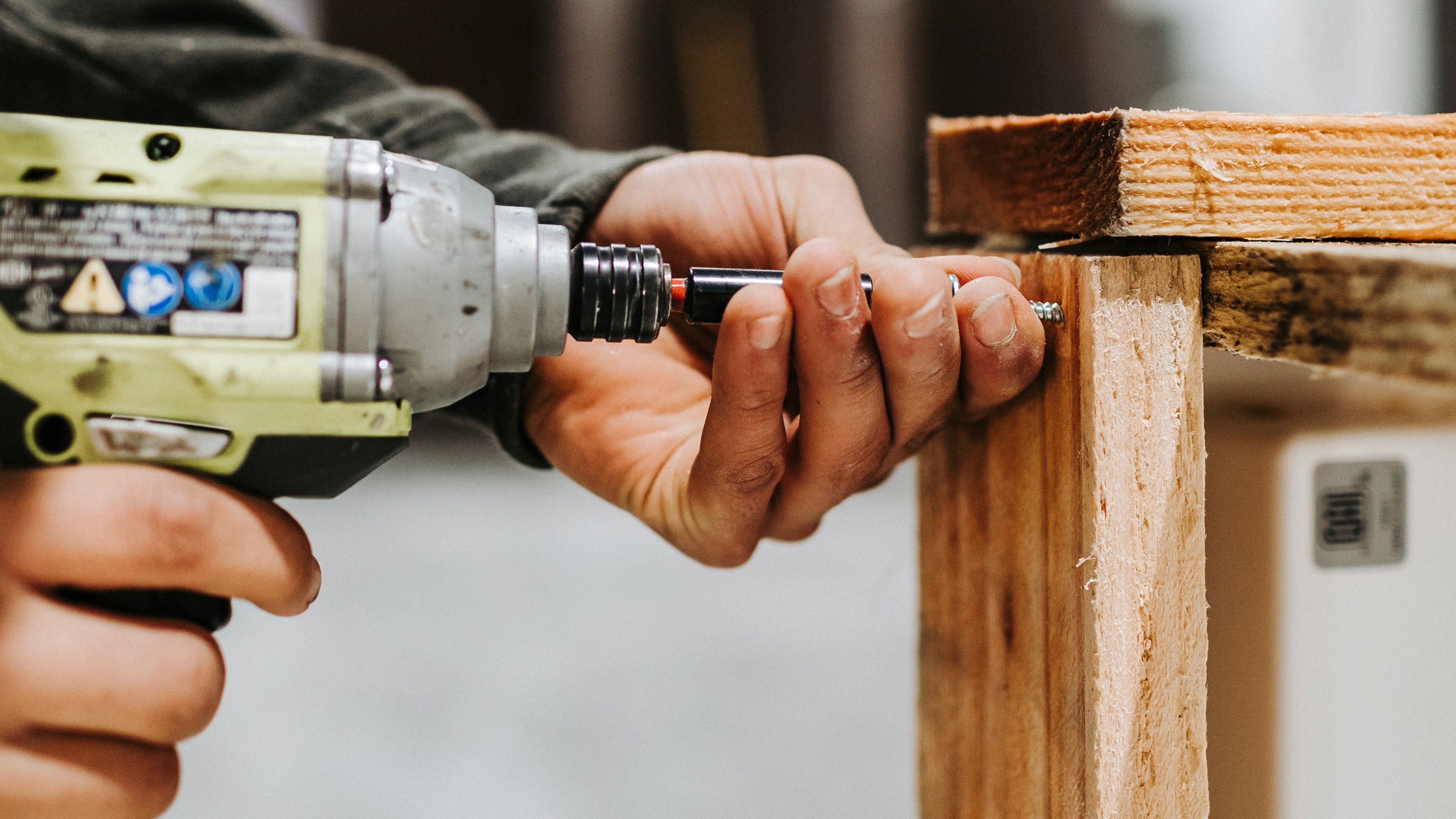
The most dangerous period of time for fiberglass shower units is the window between departure from the factory and the completion of installation. Chips, breaks, distortion, and other damage to fiberglass showers during shipping and installation can come from a variety of threats, such as:
- Rain (especially for plywood or cardboard-reinforced units)
- Impacts during loading and unloading
- Improper stacking, loading, or storage
- Bumps and bruises on the road in the logistics chain
- Drops or collisions while being carried for installation
- Damage from tools during unpacking or the installation process
These incidental sources of damage are just some of the reasons that defect rates are so high in the industry today. But delivery doesn’t need to represent such a great risk. With a carefully designed packaging solution and proper shipping precautions, it’s possible to reduce defect rates from the 10-30% experienced with many manufacturers to the less than 1% rate we have at EverFab.
Here’s how we do it.
EverFab Ships Fiberglass Shower Units Safely
- Wooden Perimeter: We always utilize a wooden perimeter in our packaging as a delivery precaution. It surrounds our fiberglass shower units and ensures that the skirt, apron, and glances are protected from potential damage.
- Bottom Board: The drain and shower floor are one of the most vulnerable areas of fiberglass shower units, and a common area for damage during the delivery process. Low-profile shower units are especially at risk. We use a strong, flat wooden board as a solid base to prevent the bottom of the unit from resting directly on the ground.
- Diagonal Support: The larger the fiberglass shower unit, the greater the risk that torquing or external pressures will damage the packaging structure—and the unit itself. It’s critical to use an additional diagonal board for greater structural strength and to preserve the integrity throughout delivery.
- Superior Material Durability: We use an advanced composite hexacomb mesh in our EverFab Core Material to reinforce every shower we make. This material gives our units incredible durability and the strength to withstand the stresses of delivery.
- White Glove Customer Service: There’s no replacement for responsive, fast, and reliable customer service during delivery. Lead times on EverFab showers are radically faster than the average in the industry, often in the range of 25% to 50% better than many of our competitors. With faster delivery and lower defect rates, our warranty rate can achieve 10 to 30 times the value you’ll get from other manufacturers. Our customers trust EverFab to get fiberglass shower units delivered sooner and in much better condition.
If this sounds too good to be true, give us a try. You’ve got to see it to believe it. Get in touch with us today and we’ll be happy to share more information on how EverFab protects your project through safe shipping, faster installation, and durability over many years of use.
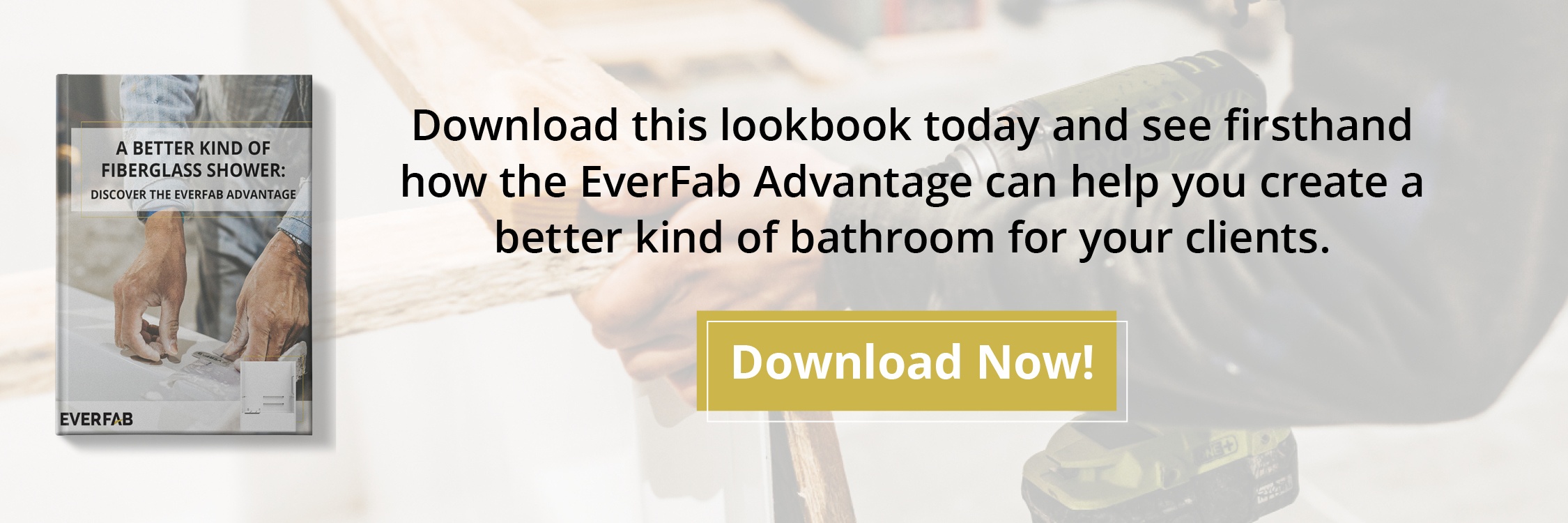